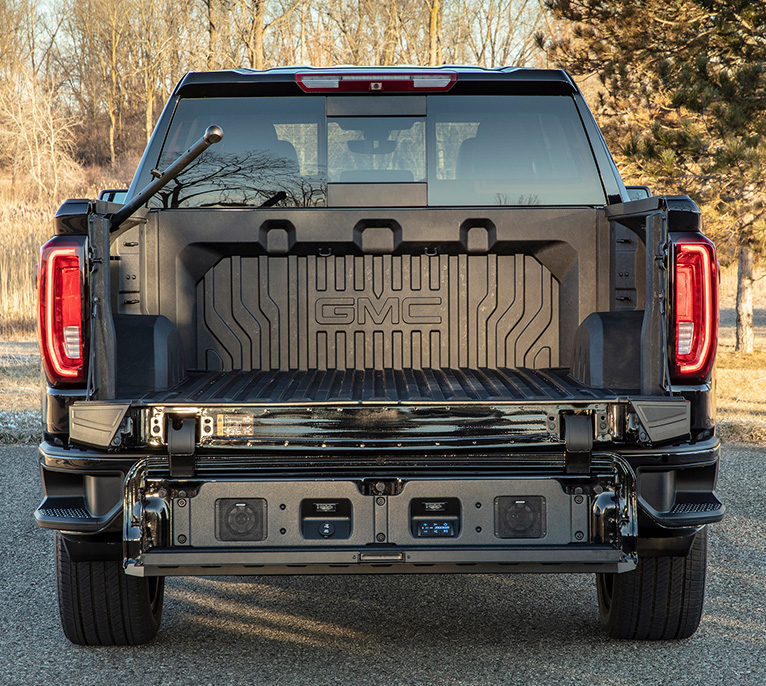
学生時代から夢見たテーマに、
アメリカで挑む。
世界中で厳しさを増している自動車のCO₂排出規制。燃費を向上させ、CO₂排出を抑える代表的な手段のひとつが、自動車の軽量化です。テイジンは2008年から、熱可塑性樹脂を使用した炭素繊維複合材料の開発に力を注いできました。のちに「Sereebo®」ブランドとして展開されるその複合材料は、自動車の構造部材として使用すれば重さは鉄の約半分。2011年頃からは、採用してくれる自動車メーカーや部品メーカーを探し始めていました。ちょうど同じ頃、まさに炭素繊維による自動車の軽量化を検討していたのが、米国のゼネラルモーターズ(GM)です。2社の思惑が一致したことで、ピックアップトラックの荷台部分を「Sereebo®」でつくるための共同開発が始まりました。
入社10年目だった私は、大急ぎでビザを取ってアメリカに渡りました。開発拠点になったのは、GM社とテイジンのメンバーが半々ずつ入居する建物。お客様であるGM社と生活をともにしながら、通訳を介することなく開発を行うという、なかなかチャレンジングな環境でした。
一方で、自動車の軽量化というテーマには非常に燃えていました。私は学生時代、改造市販車によるスプリントレースに参加していました。その時に初めて炭素繊維を知り、エアロパーツを自作してみて、軽量化の恩恵を文字通り体感していたのです。GM社とのプロジェクトは、炭素繊維がもたらすメリットをいよいよ一般車にも広げられる、願ってもない機会でした。